Summary:
The TPS43330-Q1/TPS43332-Q1 contains two current mode synchronous buck controllers and one voltage mode boost controller. This component is ideally suited as a pre-regulator stage that requires less Iq and does not require damage to the system in the event of a power outage caused by an unexpected event. An integrated boost controller allows the device to operate with input voltages as low as 2V without causing a voltage drop during the buck regulator output stage. At light loads, the buck controller automatically runs in low-power mode, consuming only 30μA of quiescent current.
The buck controller has an independent soft start function and a power good indicator. The current foldback in the buck controller and the cycle-by-cycle current limit in the boost controller provide protection for the external MOSFET. The switching frequency can be set between 150kHz and 600kHz or synchronized to an external clock in the same range. In addition, the TPS43332-Q provides frequency hopping spread spectrum operation.
Device Use Vehicle Start Stop, Infotainment, Navigation Tools Cluster System Industrial/Automotive Multi-Track DC Distribution System and Electronic Control Unit
Features Two synchronous buck controllers A pre-boost controller with an input range of up to 40V (instantaneously up to 60V), when boost is turned on, operation drops to 2V
Low power mode IQ: 30μA (one buck on), 35μA (two buck on)
Low shutdown current Ish < 4 μA
Buck output range from 0.9V to 11V
Optional boost output: 7V/10V/11V
Programmable frequency and external synchronization range from 150kHz to 600kHz
Separate start input (ENA, ENB)
Frequency Spread Spectrum (TPS43332)
Optional forced continuous mode at light load or automatic low power mode sense resistor or inductor DCR inductive buck channel for off-phase switch peak gate drive current 1.5 A
Thermally Enhanced – 38-Pin HTSSOP (DAP) PowerPadTM Package Meets Automotive Application Requirements
Integrated power controller TPS43330-Q1 data sheet, user guide see PDF document (click to download)
Surface-Mount (SMT) &BGA Assembly
What is SMT PCB assembly?
SMT patch refers to the abbreviation of a series of technological processes that are processed on the basis of PCB, and PCB (Printed Circuit Board) is a printed circuit board. SMT is surface mount technology (Surface Mounted Technology) (abbreviation of Surface Mounted Technology), and it is one of the most popular technologies and processes in the PCB assembly industry.
SMT is surface mount technology (Surface Mounted Technology) (abbreviation of Surface Mounted Technology), and it is one of the most popular technologies and processes in the PCB assembly industry. Electronic circuit surface mount technology (Surface Mount Technology, SMT), called surface mount or surface mount technology. It is a kind of surface assembly components with no leads or short leads (SMC/SMD for short, chip components in Chinese) mounted on the surface of a printed circuit board (Printed Circuit Board, PCB) or the surface of other substrates. Circuit assembly technology in which reflow soldering or dip soldering is used for soldering and assembling. Under normal circumstances, the electronic products we use are designed by PCB plus various capacitors, resistors and other Electronic Components according to the designed circuit diagram, so all kinds of electrical appliances need a variety of smt patch processing techniques to process.
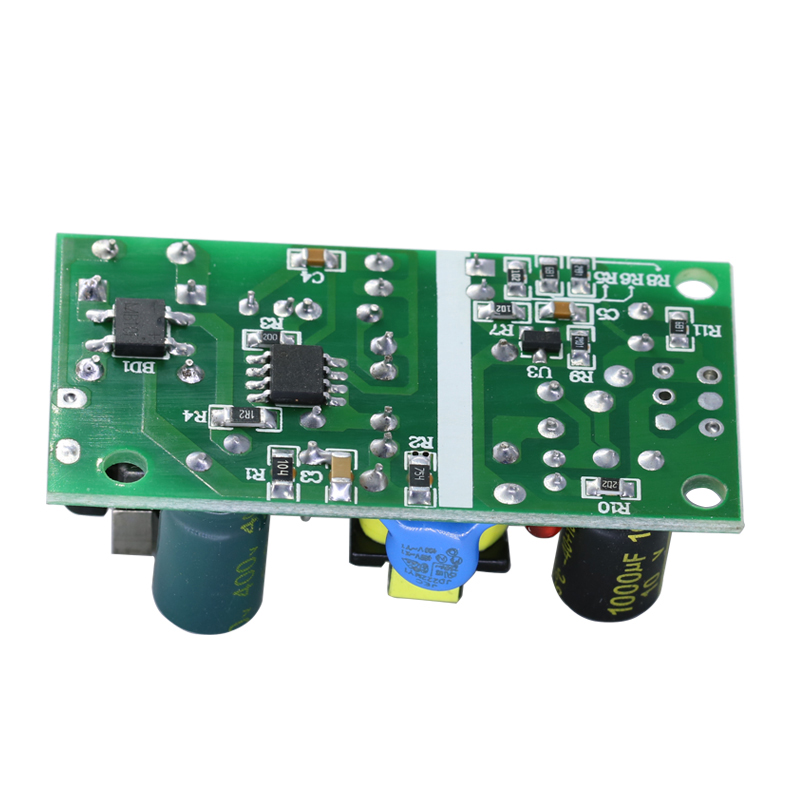
1. Silk screen: Its function is to leak solder paste or patch glue onto the PCB pads to prepare for the soldering of components. The equipment used is a screen printing machine (screen printing machine), located at the forefront of the SMT production line.
2. Dispensing: It is to drop the glue onto the fixed position of the PCB board, and its main function is to fix the Electronic Components on the PCB board. The equipment used is a glue dispenser, located at the forefront of the SMT production line or behind the testing equipment.
3. Mounting: Its function is to accurately mount the surface mount components to the fixed position of the PCB. The equipment used is a placement machine, located behind the screen printing machine in the SMT production line.
4. Curing: Its function is to melt the patch glue, so that the surface assembly components and the PCB board are firmly bonded together. The equipment used is a curing oven, located behind the placement machine in the SMT production line.
5. Reflow soldering: Its function is to melt the solder paste, so that the surface assembly components and the PCB board are firmly bonded together. The equipment used is a reflow oven, located behind the placement machine in the SMT production line.
6. Cleaning: Its function is to remove the solder residues such as flux that are harmful to the human body on the assembled PCB board. The equipment used is a washing machine, and the location may not be fixed, it may be online or offline.
7. Inspection: Its function is to inspect the welding quality and assembly quality of the assembled PCB board. The equipment used includes magnifying glass, microscope, online tester (ICT), flying probe tester, automatic optical inspection (AOI), X-RAY inspection system, functional tester, etc. The location can be configured in a suitable place on the production line according to the needs of the inspection.
8. Rework: Its function is to rework the PCB boards that have failed to detect faults. The tools used are soldering irons, rework stations, etc. Configured at any position in the production line.
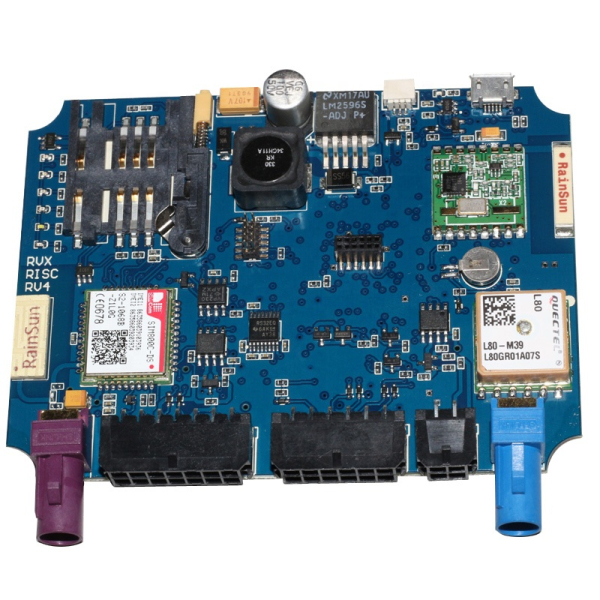
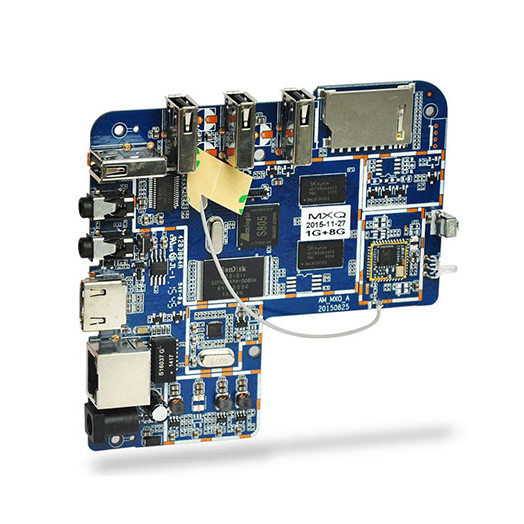
Smt Bga Assembly,Surface Mount Technology Assembly,Wireless Charger Pcba Circuit Board,Pcba Motherboard Assembly
HAODA ELECTRONIC CO.,LIMITED , https://www.pcbhdi.com